Do you want to know how to be in control of your business?
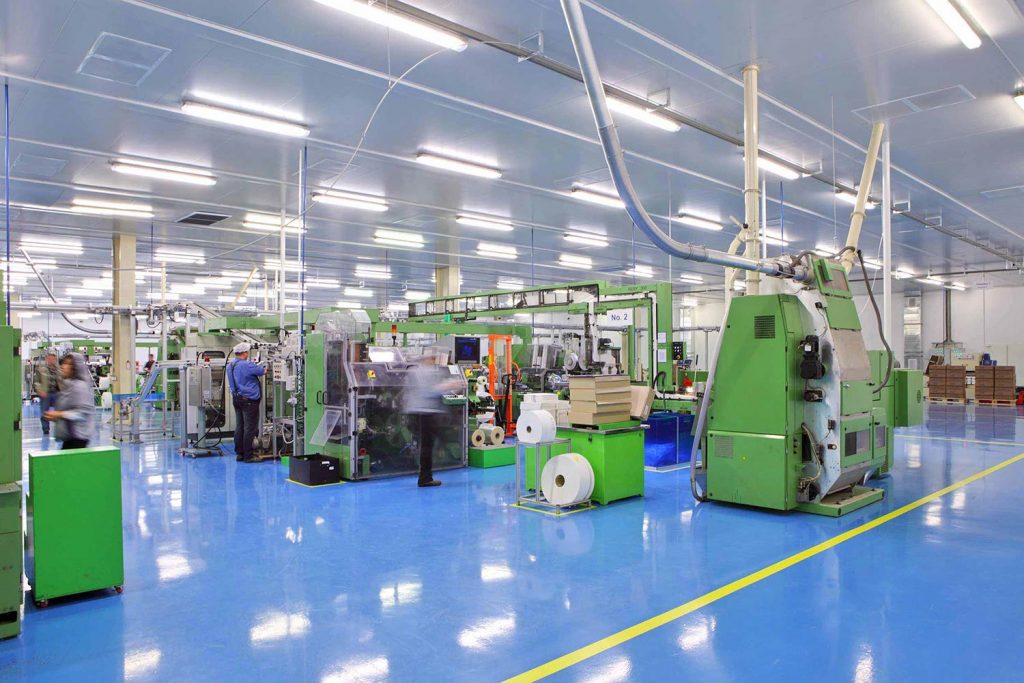
As a manager, do you want to know what’s going on in the factory?
Do you find it essential, not to lose any details of the operation?
If yes, I will show you how to easily implement an inexpensive system that assures you are in control of your business in manufacturing.
A CEO WHO DOESN’T WANT TO MEASURE
I visited a manufacturer in Hungary recently. The company operates dozens of plastic molding machines. It is a prosperous enterprise.
I asked the CEO, how they measure and monitor the energy consumption of the machines in the factory.
”We measure the total consumption of the manufacturing halls plus we know the operating hours and the rated power of the machines there. That’s enough information for us,” he answered.
I was astonished. Why is he satisfied with this level of measurement and not interested in knowing all the details of their operation?
For us, engineers, it is obvious, that you continuously measure all the parameters you can. To be frank, you gather data even if you are not able to evaluate it at the time. But maybe later on you will be able to do so… We engineers know that it is better to have abundant data than not to have data at all.
“I don’t want to establish any ’measurement system’ investing a lot of money. I’m a ‘ROI and payback man’ and I can’t see the ROI and payback period of such a system,” explained the CEO.
HOW TO CONTROL THE BUSINESS THEN?
“OK,” I said, “forget the ’measurement system’ idea for a while.”
“Can I ask another question? How do you control your company? What data do you use for controlling the business?”
The CEO explained to me that they have SAP, they know everything about the cost elements, about the purchasing activities, stock and so on. The CEO stressed that without an ERP system no company can exist these days.
“I understand. What about the manufacturing processes? How do you control them? How do you collect information about the status of your machines?” I continued.
Silence.
Well, well. Isn’t it strange that you can’t live without an ERP system but in the case of manufacturing you are happy that you have outsourced the maintenance activities and you don’t receive any real-time information about the production that generates your profit?
“I know,” said the CEO, “that it would be perfect to connect all the machines to a data network and to have all the data real-time, but it is hard to justify that huge amount of investment. Plus, we have different machines from different suppliers, it would take lots of energy and resources to connect the entities.”
Let’s stop here for a moment and stick a pin in it.
Now we have agreed that it is useful to have real-time data about the manufacturing entities. The goal is to monitor and control the entities in the manufacturing halls. It is clear that the all-pervasive solution is too expensive. Does that mean that there’s no good solution? Of course not.
Let’s find other ways to reach the goal with a good cost/benefit ratio.
A SOLUTION
Why not try this method?
What if you set up a network which continuously monitors the status of the entities through their pattern of energy consumption?
At first glance it may not be obvious how much information you can gather this way. But think of the electrocardiogram (ECG). Our concept is very similar to the ECG which is used to detect heart problems. ECG is a well-established practice, its values are unquestioned.
Our system registers all the tiny changes in current and voltage values on the load (machine) and displays the details of the performance of the machine.
A performance pattern makes sense only when and if it can be compared to a reference value. If you have dozens of similar entities deployed in a manufacturing operation that is exactly the case.
What comparisons are at hand?
The system
- compares the performance of similar units and searches automatically for differences,
- stores timelines and detects deviations,
- gives warnings when the preset values are exceeded,
- can identify and store deterioration patterns for breakdown prevention,
- can intervene remotely and switch on/off circuits by command.
Another advantage of our system is that the installation doesn’t affect the warranty of the machines, our power quality analyzer devices are easily installed in the main distribution cabinets of the manufacturing halls.
“Now I understand the concept fully and acknowledge the advantages,” said the CEO. “If the total cost of ownership is reasonable we can launch a pilot.”
I have the competitive analysis on my desk, I definitely know that our technology is superior to the competitors’ and our prices are significantly lower.
I know that based on our experience the system will pay back the investment in 6-12 months.
“Let’s do it,” we agreed.
Leave a Reply